To
allow the implant to be improved and made accessible
to more people it was necessary for it to become a commercial
enterprise. Commercialisation of the cochlear implant
was essential if it was to be an economically viable
project. However the Australian market was too small.
Nucleus
Ltd
Nucleus Ltd, a group of companies that manufactured
highly developed medical equipment, won a tender to
"carry out a market survey and cost development
plan for the cochlear implant". (Epstein, 1989:
51)
The
four member team responsible for the plan worked on
two tasks:
- research
overseas to study market potential
- a
review of the cochlear implant system design
resulting in a simplified version featuring a single
integrated circuit.
In
1981, with the University of Melbourne and the Australian
government, Nucleus set out to develop a commercially
viable cochlear implant and to carry out a worldwide
clinical trial.
Reports
were written for both tasks and presented to the Australian
government. Nucleus Ltd was awarded the contract to
develop the cochlear implant.
Cochlear
division of Nucleus
Paul Trainor, Chief Executive Officer, Nucleus Ltd,
formed the Cochlear Division of Nucleus he then
selected a three member Tiger Team.
A Tiger Team, according to Trainor's philosophy, was
a small single-minded group moving forward very quickly
on a specific project and as far as possible not distracted
by the usual day-to-day commitments of a job. They
were relieved of much of the bureaucracy and administration
so that they could concentrate on the main task, and
they were given fully equal or rotating responsibility
for accelerating the work. Naturally, as the project
matured so did the necessity for red tape and administrative
practice, but at the beginning freedom for the job
itself was all important. So the small team began
and at first constructed the device by hand, acting
as designers and manufacturers and checking each other's
work for quality control. (Epstein, 1989: 53)
The
team increased in size and each member was responsible
for a component. The implant was broken down into:
- implant
system design
- integrated
circuit design
- promontory
simulator: a test which demonstrated whether the nerves
of the inner ear were working properly.
- speech
processor: received, processed and stored information
in a way appropriate to each individual implantee.
- external
electric components
- automatic
gain control device: necessary to expand or compress
incoming sounds to an acceptable level.
- electrode
array
- implantable
stimulator. (adapted from Epstein, 1989: 53)
Refining
the mechanics of the implant
A newly emigrated Polish mechanical engineer, Janusz
Kuzma, was responsible for the mechanical aspects of
the implant. He
had
to devise a way of sealing (the implant) hermetically
with biocompatible material as well as incorporating
a mini antenna coil to pick up the signals. He solved
the latter problem by looping the coil outside the
small round device and enclosing the whole in soft
silastic. A new electrode system with 22 electrodes
had to be accommodated, and he was also responsible
for the design of the external headset. He knew the
electronic parts would not function correctly unless
the mechanical parts were perfect. He knew the team
was dependent on and accountable to public funds.
He knew there was a time limit and time was running
out. He had many sleepless nights.
(Epstein,
1989: 54)
Building
on the University of Melbourne research, Cochlear developed
the more advanced 22 channel implant and the wearable
speech processor (WSP). The design philosophy was to
make a flexible cochlear implant with sophisticated
sound processing in the externally worn speech processor.
This allowed the recipient to take advantage of improvements
in technology without surgically replacing their implanted
device.
Twelve
months after the team began it had managed to completely
redesign the whole cochlear implant system and develop
an implantable device. The system was ready for clinical
trials.
Clinical
trials overseas
Clinical trials of the Australian cochlear implant were
set up in Australia and overseas. Competition in electronic
engineering and microchip technology in medical devices
was world wide and the Australian government wanted
to capture some of the overseas market.
For
the Cochlear implant to be available to the American
market, and indeed world wide the US Food and Drug Administration
had to give its official approval. This was achieved
in 1985.
Cochlear
Ltd today
Since 1988, Nucleus, including Cochlear, had been a
wholly owned subsidiary of Pacific Dunlop. In 1995,
Cochlear was sold by Pacific Dunlop and floated on the
Australian Stock Exchange, as a publicly listed company.
The
Nucleus® 24 Contour implant won the Australian
Design Award of the Year in March 2000. It
has some important features:
- an
electrode that is curved before insertion into the
cochlea
- it
places the electrodes closer to the important parts
of the cochlea
- does
not exert any force on the bone or tissue after it
is inserted.
Engineering considerations
Some significant engineering considerations were addressed
in the development of the Nucleus® 24:
1. |
Easy
insertion
Ability to insert a pre-curved electrode array
that is designed to fit inside the inner wall
of the human cochlea and has a coating which is
moulded from silicone into the correct shape.
To insert the electrode into the cochlea it is
temporarily held straight using a fine wire stylet.
Once inserted, the stylet is removed. The electrode
must be flexible enough to move around the cochlea
without causing trauma and have sufficient memory
to return to its original curved shape. The stylet
also must be easily removable and all components
must be easily manufactured.
|
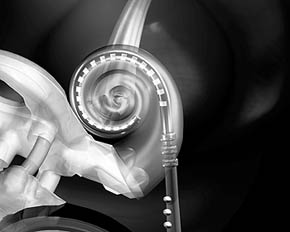
Simulation
of contour insertion (New York University)
|
|
2. |
Biocompatibility
The implant is made from titanium, silicone rubber
and platinum. The sophisticated electronic sub-assembly
is encapsulated by the titanium shell. The electronic
package is connected to the electrodes by insulated
platinum wires about 25 microns in diameter. The
electronic package is implanted into the mastoid
bone in the skull. The titanium shell must prevent
bodily fluids from entering the package, but also
have a connection to the 22 electrode array and
the radio frequency antenna outside the package.
The device also needs to be strong enough to withstand
surgery and implantation and subsequent flexing
for its design life of 70 years.
|
3. |
Long
term reliability
The implant is guaranteed for ten years but designed
for a life of 70 years. |
4. |
Safety
during insertion and after receiving the implant
After implantation the processor and system must
be customised for each individual. During programming
of the device it is important that the recipient
is not exposed to excessive stimulation which could
be painful. |
5. |
Ease
of manufacture
The implant is handmade under a microscope. |
Manufacture
of the cochlear implant
Production
of the speech processor
The behind-the-ear (BTE) speech processor differs
from a conventional body-worn speech processor,
as it contains a directional microphone, contained
within the same case as the speech processor unit.
The production processes for each processor are
very similar.
|
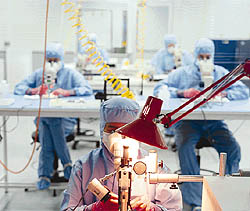 |
Precision assembly of the
cochlear implant (Cochlear Pty Ltd) |
|
1. |
The
ten-layer, double-sided circuit board, which is
the heart of the body-worn processor, is mounted
with six integrated circuit components as well as
capacitors, transformers, resistors and other components.
|
2. |
A
pick and place machine is employed to automatically
place and solder components to the gold pads on
the board, according to a program that is loaded
for each different circuit board configuration.
The push button switches, which are eventually operated
by the external buttons, are manually soldered to
the board, as are connectors (which are used to
connect cables to the test system during testing),
a lithium battery and a power transformer. |
3. |
The
circuit board, which is made up of flexible and
rigid parts, is tested and then fixed to the plastic
casing. |
4. |
The
control panel, with buttons and LCD window is assembled
onto the moulded plastic case. |
5. |
The
closed processor is tested to ensure that the circuit
is functioning correctly, before it is baked overnight,
and then re-tested. |
6. |
The
small double-sided circuit board of the BTE processor
contains a custom integrated circuit, which is protected
by a blob of semiconductor coating, and other components.
The microphone, potentiometer (an adjustable resistor
which is seen as the dial from the outside), and
switch, are soldered to the populated board and
everything is placed into the case. |
7. |
The
RF socket and the battery terminals are connected
to the circuit, before the board is coated. |
8. |
The
closed processor is tested, before the cover and
the ear hook are attached. |
Production
of the cochlear implant
The Cochlear implant itself is made up of three
main functional components:
1. the stimulator
2. the antenna coil and
3. the electrode unit.
The
heart of the stimulator is the Cochlear implant
chip, an integrated circuit. The stimulator also
contains a ceramic disk, or feedthrough, with
twenty-four platinum pins to which each of the
twenty-two electrode wires, and two coil wires,
are attached in the final assembly. The stimulator
is responsible for picking up the signals from
the antenna, and sending out the appropriate electrical
energy to the electrodes. The stimulator is encased
in titanium shells, which are laser welded together.
The
antenna coil, which forms the loop of the implant,
is welded to the stimulator, to form a functional
antenna. It is then wound into the shape that
you see in the final implant. An extracochlear
electrode is assembled, using fine platinum wire,
and is also attached to the stimulator. Stimulator
components are prepared and cleaned prior to entering
the clean room. All antenna coil assembly is conducted
in the cleanroom.
|
|
Most
of the assembly operations for the behind-the-ear
speech processor and the stimulator assembly
are done under a microscope. In the stimulator
production and external production areas,
controls are in place to protect the statically
sensitive devices being handled, therefore
operators wear special lab coats, wrist and
heel straps for grounding, and gloves.
(Cochlear Pty Ltd)
|
|
The
cleanroom is a totally controlled environment
with set temperature and humidity levels, where electrode
assembly and final implant assembly takes place. Strict
controls are required during the final assembly of implants
to ensure that the final product is clean, and after
sterilisation, ready for implantation. Full body garments
are worn in the cleanroom, from boots, overalls, hood,
mask and gloves.
The
electrode unit can either be made up of a straight electrode
array or a contoured array.
1.
|
Each
platinum electrode wire is welded to a platinum
ring. The wires are fed through the rings, and one
at a time, each wire is attached to one ring. A
lead wire is attached and the whole thing is encased
in silicone. |
2. |
This
electrode unit is attached to the stimulator, and
the individual wires are attached to the corresponding
pins on the stimulator. |
3. |
The
assembly is electrically tested and then silicone
is injected to insulate the stimulator. |
4. |
The
outside titanium shell is laser welded to the stimulator,
and the unit is tested again. |
5. |
The
implant assembly is baked overnight in a vacuum
oven, and then undergoes final hermetisation, which
means that the small hole in the stimulator shell
is fused resulting in a gas-tight seal around the
stimulator. |
6. |
A
small magnet is then inserted in the outer moulding
and the entire implant assembly is placed in a moulding
die into which silicone is injected, to completely
encase the implant. |
7. |
The
implant is bent so that the coil is at an angle
to the stimulator and the magnet is removed. |
8. |
The
implant is washed, the magnet reinserted, and the
assembly is electrically tested. |
9. |
Finally
the product is packed in a sterile pouch, this complete
assembly is sterilised, and the implant is packed. |
This
is a basic overview of the manufacturing processes involved
in producing the components necessary for a functional
Cochlear implant system, which transmits signals from
outside the body, to the electrode inside the cochlea,
allowing the recipient of the implant to hear. Text
provided by Cochlear
Pty Ltd.
Design process
The following two diagrams illustrate the design process
flow. They incorporate the philosophy of plan, do, check,
act used by Cochlear Pty Ltd.
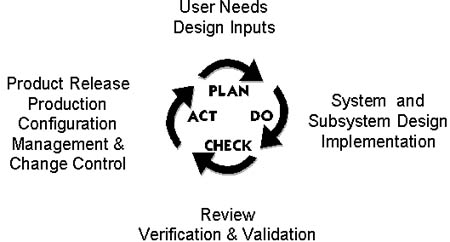
Process
flow (Cochlear Pty Ltd)
Design process flowchart indicating the stages involved
in developing a product. Note the tollgates or check
points throughout the process. (Cochlear Pty Ltd) Click
image to view enlarged version.
Tollgates
At significant points in the design process Cochlear
has set up tollgates or check points where approval
from a management team is required before the process
can continue. Refer to the design process flowchart
when considering the information in the table.
Tollgate
|
When it occurs
|
Approval to proceed to:
|
1 |
Project
start |
System
development |
1A |
Completion
of system design |
Design |
2 |
Completion
of detailed design |
Process
development |
3 |
Completion
of implementation |
Pilot
production |
4 |
Completion
of pilot production, Clinical trials |
Production |
5 |
Completion
of market stability assessment |
Sustaining
engineering |
|