 |
 | |
 |
|
I can make one widget in my workshop or my kitchen, but how could
I make thousands of them? I'd need a factory, well trained people, machines,
reliable supplies of raw materials, a system to manage production, and
a testing process to check that quality stays high.
|
|
|
 |
|
Making many copies of a product is called mass production.
It begins with raw materials of consistent content and properties, uses
various machines and processes to transform them into the desired products,
and packages the products for distribution and sale.
Manufacturing usually takes place in a factory designed
to move the raw materials to the machines to be processed in the correct
sequence. People, robots, computers and conveyor belts make this happen.
People maintain the machines and manage the whole process.
The designed shape is transferred to materials via custom-made
moulds, dies, jigs, and cutting tools, collectively called tooling. Materials
might need to be cut, melted, shaped, and joined. Surfaces might need
to be finished by painting, polishing, or affixing decals.
Quality assurance is important in manufacturing. It involves
checking the raw materials, inspecting the product at various stages of
manufacture, and checking the finished product. Checking can involve visual
inspection, machine scanning, weighing, testing physical properties in
a laboratory, and operating to ensure that a part or product functions
correctly.
Manufacturing requires large financial investment to set
up and to introduce innovation. Attention is paid to reducing costs such
as the amount of energy and material used to make each product. Retaining
workers through enterprise agreements and good workplace practices, such
as occupational health and safety, reduces costs associated with training
new workers.
Mass Production and Henry Ford http://www.spartacus.schoolnet.co.uk/USAmass.htm
|
|

|
|
Caroma
dual flush toilet made in quantity while maintaining quality
Caroma led the world in making dual flush toilets, which
use less water and produce less sewage than conventional
toilets. Because of this innovation, backed up by substantial
investment and a commitment to quality, Caroma has become
a successful exporter.
One Caroma factory makes vitreous china toilet pans and
cisterns, the main raw material being clay. The moulds
are complex, and the process takes several days, as the
wet clay dries slowly and is then glazed and fired in
a large kiln. Another factory makes plastic cistern parts,
plastic toilet seats, and some plastic cisterns. The processes
used for making the plastic parts are injection moulding
and compression moulding.
The work is carried out by people and robots, presses
and conveyor belts. All processes are closely monitored,
and samples are taken regularly for testing. The plastic
valves are all tested as they are made, and the completed
cisterns are filled with water to test that they flush
correctly and don't leak. The factories are registered
with the international standards organisation, and visited
regularly by independent inspectors, to demonstrate that
they follow world's best practice.
The company has also attained registration affirming that
it meets world's best practice in environmental management,
using materials and energy efficiently and not producing
dangerous wastes.
Attaining registration for both standards was a long and
difficult process that required people to change their
thinking. And maintaining the standards requires constant
careful management of all aspects of manufacturing.
The introduction of a new toilet to production is a complex
process, but continuing innovation is essential. Marketing,
R&D and manufacturing departments are all involved,
and management must give approval before money is spent
on the expensive tooling needed to mass-produce parts
for the new product.
| |
 |  |
|
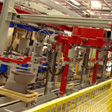 |
Caroma's Sydney factory. Courtesy of Caroma Industries Ltd |
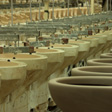 |
Close-up of production line. Courtesy of Caroma Industries Ltd |
|
|
Introduction
Flush toilets have been in use for over 200 years. They
make our lives more pleasant by flushing bodily wastes
away, and thus reducing our exposure to bad smells and
nasty diseases. Imagine living in a crowded city without
a sewerage system!
However, the traditional WC (water closet) used a lot
of water. This meant that a lot of water had to be supplied
and a large volume of sewage had to be piped away and
treated.
Before Caroma began developing the dual flush toilet,
the average Australian toilet used about 11 litres of
water for each flush. Some companies made toilets with
two flush volumes, but without separate buttons; they
were difficult to operate and often failed to flush properly.
Now most new toilets made in Australia use only 6 litres
(full flush) or 3 litres (half flush).
Caroma owns factories in Sydney, Melbourne and Adelaide.
It makes baths, basins and bathroom accessories as well
as toilets.
| | |
|
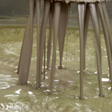 |
Slip ready for use. Courtesy of Caroma Industries Ltd |
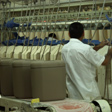 |
Greenware cisterns, with moulds in background. Courtesy of Caroma Industries Ltd |
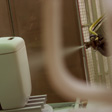 |
Robot spraying glaze. Courtesy of Caroma Industries Ltd |
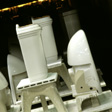 |
Toilet pans and cisterns emerging from the kiln. Courtesy of Caroma Industries Ltd |
|
|
Making
vitreous china toilets
Most toilets are made from vitreous china. Vitreous means
glassy: the china has a strong atomic structure that makes
it waterproof and resistant to damage, and a smooth surface
that is easy to clean. Caroma manufactures all its pans,
and most of its cisterns, from vitreous china.
The raw material is clay, which is obtained from quarries
in Victoria, bagged, and trucked to factories in Melbourne
and Sydney. At the factory, it is delivered to the 'slip
house' and fed into ball mills, large rotating drums containing
loose steel balls that crush the clay. The crushed clay
is sieved and mixed with minerals, fluxes and water to
make 'slip'.
Each factory makes several different designs of toilet
pan and cistern, as well as china basins. Each design
has a unique 'original mould' crafted for it. This is
copied to make many 'production moulds'.
The mould for a toilet pan is quite complex and is made
in several pieces, which are clamped together before use.
Slip is poured into the mould and left to set for about
an hour. The plaster mould absorbs water from the slip
during this time.
Next, the mould is unclamped and the resulting 'greenware'
is dried over three days. Drying begins in the open space
of the factory, assisted by many fans, and finishes in
a large dryer. If items are not properly dried they can
explode in the kiln!
Hot air is pumped into the factory at night to dry the
moulds. Each production mould can be re-used about 100
times.
The next step is glazing, to give the surface its smooth
and shiny finish. The glaze, composed mainly of silica
(silicon dioxide) and nepheline (a silicate mineral),
is made in the slip house. A small amount of green vegetable
dye is added. A robot sprays the glaze onto each item
as it is brought to it on a conveyor belt. The green dye
allows the robot to sense which parts of an item have
been sprayed and which are yet to be sprayed.
The items are then stacked on kiln cars to carry them
into the tunnel kiln for firing. They take about 20 hours
to move slowly through the kiln, being heated gradually
to 1200°C in the central zone, then cooling gradually
before they emerge. In the hot zone, the vegetable dye
vaporises and the slip and glaze vitrify. The material
shrinks as it vitrifies, but it maintains its shape.
The next step in making a cistern is to assemble the plastic
components inside it. Most are made in Caroma's Adelaide
factory and trucked to Melbourne and Sydney. A few are
made by other companies.
At every point in the production process, the items are
individually checked. Once the cistern is assembled, it
is filled with water to check that it fills and flushes
correctly and does not leak.
Making ceramic moulds
http://www.www.ferringallery.com/gallery/thayer/articles/ceramicstechnical.html
How to make a two-piece mould http://www.garlic.com/~7Eblufrogg/dolls/mold.htm
Sanitaryware models, moulds and cases http://www.sacmi.com/English/ceramic/pdf/modelling.pdf
| | |
|
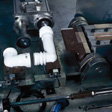 |
Automated production of plastic pipe. Courtesy of Caroma Industries Ltd |
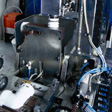 |
Injection moulding machine. Courtesy of Caroma Industries Ltd |
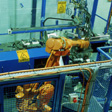 |
A robot at work in Caroma's Adelaide factory. Courtesy of Caroma Industries Ltd |
|
|
Making
the plastic parts
In addition to the plastic cistern parts, the Adelaide
factory makes plastic seats and cisterns. Most of the
plastic is sourced from formulators in Victoria; a small
amount is imported from overseas and compounded locally.
The appropriate plastic is chosen for each part. Two fabrication
processes are used by Caroma: injection moulding and compression
moulding. Each mould (also called a tool) can be used
to make millions of parts.
Injection moulding tools are made of hard steel, with
their surfaces hard chromed. To make a part, thermoplastic
granules are poured into the mould and subjected to heat
and pressure. It takes only seconds for each part to be
made.
One process that has been fully automated is assembly
and testing of the valves that control water flow in the
cistern; if a valve fails the test, it is disassembled
and usually reassembled. This is all done just a few seconds
after the valve parts are made, so any recurring problems
noted in testing can be addressed quickly. Automating
this process took many years of research and development.
Compression moulding is used to make toilet seats because
consumers like the solid feel of thermoset plastic, which
cannot be injection moulded. Enough granulated plastic
is spread inside the mould to slightly overfill it. The
powder is heated to 145ēC. The mould is closed and subjected
to pressure of 400 tonnes. The plastic flows to fill the
mould, with the excess squeezing out (rather like toothpaste).
The lid is made in a separate mould.
Then the seat and lid must be hinged together. Most are
assembled by hand, but one production line has a single
robot taking the whole process from raw material to packaged
product.
Simple diagrams of plastics manufacturing http://www.plastiquarian.com/manufact.htm
| | |
|
|
|
Packaging
the product
In many factories, packaging is a highly automated operation,
with robots doing most of the work. At Caroma's vitreous
china factories, where the products are heavy, breakable
and varied, they are mostly handled by people. After a
final inspection, the products are packed in cardboard
boxes and stacked on pallets.
The plastic toilet cisterns and seats are also mostly
packed by people. More robots will probably be introduced
in the future to automate this part of the factory's operation.
| | |
|
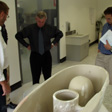 |
Caroma staff discussing a new design. Courtesy of Caroma Industries Ltd |
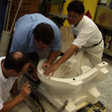 |
Skilled craftsmen modifying
the trial mould. Courtesy of Caroma Industries Ltd |
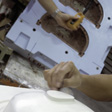 |
Adding final touches to a case. Courtesy of Caroma Industries Ltd |
|
|
Introducing
a new product
W hen Caroma developed the first dual flush toilet, new
design was combined with old. In contrast, the 6/3 litre
toilet was designed from scratch. This made it a more
satisfying project for those involved, but it cost millions
of dollars. It was not just the cistern that had to be
redesigned; the shape of the pan also had to be changed
to ensure the toilet flushed properly.
A new toilet design is first discussed by the marketing
and R&D departments. An industrial designer uses computer-aided
design (CAD) to produce images to fit the concept. The
product is market tested by showing images to potential
buyers.
A model maker mocks up the design in plaster, and then
spray paints it so that it looks like the real thing.
This is used for more market testing, and changes are
made if necessary. The design must be approved by in-house
committees and finally by company executives before going
into manufacture.
An oversized model is then made. It is oversized to account
for the fact that greenware shrinks when it is dried and
fired: each linear dimension shrinks by 11.8%, the major
change occurring in the kiln.
The model is used to make a plaster mould. This 'trial
mould' is taken to the trial cast room in the factory.
The expert modellers there pick up and resolve problems.
They make trial pieces (toilet pans and cisterns) using
the mould and send them to the main kiln to be fired.
When they are happy with the modified mould, it becomes
the 'original mould'.
If you think of the final product as positive, the original
mould is negative (it fills the space immediately around
the product).
The original mould is returned to the R&D department,
where it is used to make a resin and fibreglass 'case'.
This is positive, being the shape of the product surrounded
by a gap the shape of the mould, then more resin to form
the outside shape of the mould. The case will be used
to make thousands of plaster production moulds.
An engineer in R&D prepares control documents, which
are dimensioned drawings for the Quality Assurance (QA)
department to follow when checking samples from the production
line. And a technical writer prepares detailed information
for buyers and installers.
In Adelaide, the company makes a major change to the internal
design of the cistern parts about once in ten years, but
makes minor changes about once a month. All design for
new parts is done in-house using a high-level CAD program
called CATIA. There are no longer any drawing boards in
the design office.
An external consultancy uses Moldflow (software developed
in Australia to simulate plastic flow) to optimise the
design of each new tool. This is extremely worthwhile,
as tools are very expensive. The modified CAD data are
then used to make the tool.
We are pushing the parameters of our process
very hard and looking for very small percentage gains.
John Eagle, Engineering Services Manager, Caroma (Adelaide)
| | |
|
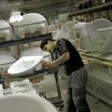 |
Each product is carefully inspected. Courtesy of Caroma Industries Ltd |
|
|
Quality
assurance
The company aims to make its products using world's best
practice. It demonstrated this commitment by attaining
ISO 9001 registration, and it works hard to maintain accreditation.
Experts from Quality Assurance Services (QAS), a subsidiary
of Standards Australia, visit twice each year to audit
the process.
The ISO 9000 family of standards represents an
international consensus on good management practices
with the aim of ensuring that the organization can
time and time again deliver the product or services
that meet the client's quality requirements.
International Organization for Standardization
Achieving ISO9001 registration took about a year. It involved
following set procedures, changing some processes, and
monitoring product quality. The main change needed was
in people's thinking.
A major, long-standing aspect of quality assurance (QA)
is constant checking of materials. The Sydney QA lab is
beside the slip house and samples every batch of slip.
It has its own tiny kiln for test firing. Laboratory staff
carry out a range of tests, including specific gravity,
flow characteristics, thermal analysis, colour checking,
water absorption, and susceptibility to crazing.
The QA staff also select finished toilets from the production
line to be tested. These toilets are taken to a laboratory
in the R&D department, which follows procedures set
by QAS or an overseas body. For example, it tests the
amount of splashback and the efficacy of flushing. The
lab is registered with the National Association of Testing
Authorities, which means its methods are so rigorous that
it does not need to send samples to other labs for further
checking.
Caroma's R&D manager, Dr Steve Cummings, sits on a
US standards board and is involved in discussions about
international standards. This type of involvement by companies
usually ensures that standards are realistic and that
standards evolve as product innovations are introduced.
Workers carry out a visual inspection of each piece after
firing and condemn those with unacceptable flaws. They
also enter details of any minor problems into a computer,
so that any trends can be traced back and the process
fixed. The R&D department does production troubleshooting.
Barcoding is being trialled in Sydney, and its full introduction
will allow the history of each piece (which batch of slip
it was made from, who dismoulded it and when, and when
it was fired) to be kept with it and retrieved at any
time.
Barcoding is central to QA at the Adelaide factory. QA
auditors routinely use handheld devices to read barcodes
and send the information via radio communication to a
central computer. The auditors also enter notes on the
devices and send them to the computer to be linked to
the barcodes for quick analysis of production problems.
QA just makes good sound business sense, and
we didn't go for ISO registration because someone
told us to, but because it fits in with our philosophy.
John Eagle, Engineering Services Manager, Caroma (Adelaide)
International standards organisation http://www.iso.ch/iso/en/ISOOnline.openerpage
| | |
|
|
|
Managing
energy and waste
The company has achieved ISO 14001 registration, which
means that it uses best environmental practice. As with
ISO 9001, registration took lots of work and needed people
to change their thinking.
The plaster from worn out moulds can be re-used. Water
is reused in the slip house and is not pumped off site.
After drying and dismoulding, pans and cisterns are inspected
by people. Any greenware that fails this check is sent
back to the slip house so that the material can be reused.
Once pieces have been fired, those that fail QA checks
are ground up and the material is used in making roads,
as there is no way of recycling vitreous china.
Waste thermoplastic from the Adelaide plant is sent to
another company to be reprocessed and returned to Caroma
for use. Recycling schemes can only work if there is a
market for their products; Caroma supports recycling by
buying plastic from several reprocessing companies to
make cistern parts.
Waste thermoset plastic cannot be recycled. As it is made
from urea and formaldehyde, two simple organic substances
that are commonly used in fertilisers, the waste material
is sold for that purpose.
Making vitreous china is an energy-intensive process,
so improvements in energy efficiency can lead to significant
cost savings and reduced environmental impact. The gas
supply company and independent consultants have helped
improve energy efficiency at the Sydney factory.
| | |
|
|
|
Managing
people
The Caroma factories employ hundreds of people, so managing
people is just as important as managing materials and
processes.
The company has negotiated enterprise agreements with
unions that set out pay, conditions and responsibilities
of management and workers. The aims of these agreements
are to improve the quality of working life and job security
of employees while improving the competitiveness of the
company.
One way in which the quality of working life is improved
is by providing a healthy and safe working environment,
safety equipment and ongoing safety training.
The company also provides training to improve and broaden
skills, with the aim of improving productivity, efficiency
and flexibility while providing a career path for workers
prepared to become multi-skilled. Caroma, like most Australian
manufacturers, employs many people from non-English-speaking
backgrounds, and training must be tailored to their needs.
The
impacts
Caroma led the world in making dual flush toilets. Now,
many countries require dual flush toilets to be installed
in new buildings. This has led to a huge saving in water
use and the amount of sewage generated. In some cases,
the building of new dams and sewerage works has been deferred
because of this reduced demand.
This innovation has also led to an increase in the number
of people employed by Caroma and its (mostly Australian)
suppliers, and in export income for Australia. Toilets
are not an obvious export item for Australia, being fairly
labour-intensive to make as well as costly to transport.
Because we have the invention in dual flush,
we are seen as world leaders and can sell into the
world marketplace.
Dr Steve Cummings, R&D Manager, Caroma (Sydney)
| | |
|
 |
  |
|
|
|